Minimalistic Horizontal Burrowing Robots
Publication: Journal of Geotechnical and Geoenvironmental Engineering
Volume 149, Issue 4
In this abstract, we report research on a bio-inspired, minimalistic horizontal burrowing robot, demonstrate its burrowing characteristics in glass beads, and test the hypothesis that breaking symmetry via robot shape and/or kinematics leads to net burrowing advancement. The robot is 33 mm in diameter and consists of a pair of 3D printed sections and a tip with various shapes [Fig. 1(a)]. The base of the tip is a 11 mm-thick flat disc, to which an additional cone or lefthanded auger can be mounted. The probe consists of a 132 mm-long back section that is partially inserted into the 86 mm-long front section with an overlapping length of 32 mm. The back section contains a linear actuator (Actuonix L16-50-63-12-P) that is connected to the front section, which contains a gear motor that is also connected to the tip. The linear actuator extends and contracts along the axial direction, while the gear motor rotates at various speeds in different directions. Horizontal burrowing tests were conducted in a clear Plexiglas rectangular box (600 length × 180 width × 300 mm height) filled with pluviated dry glass beads [Fig. 1(b)]. The movement of the robot was measured using two vertical steel tubes (dia. = 3.5 mm) connected to the front and back sections. The steel tubes added resistances of similar magnitude but in opposite directions to both sections during both the extension and contraction phases. The tubes may have resulted in less movement of individual sections, but their overall effect on symmetry breaking was negligible.
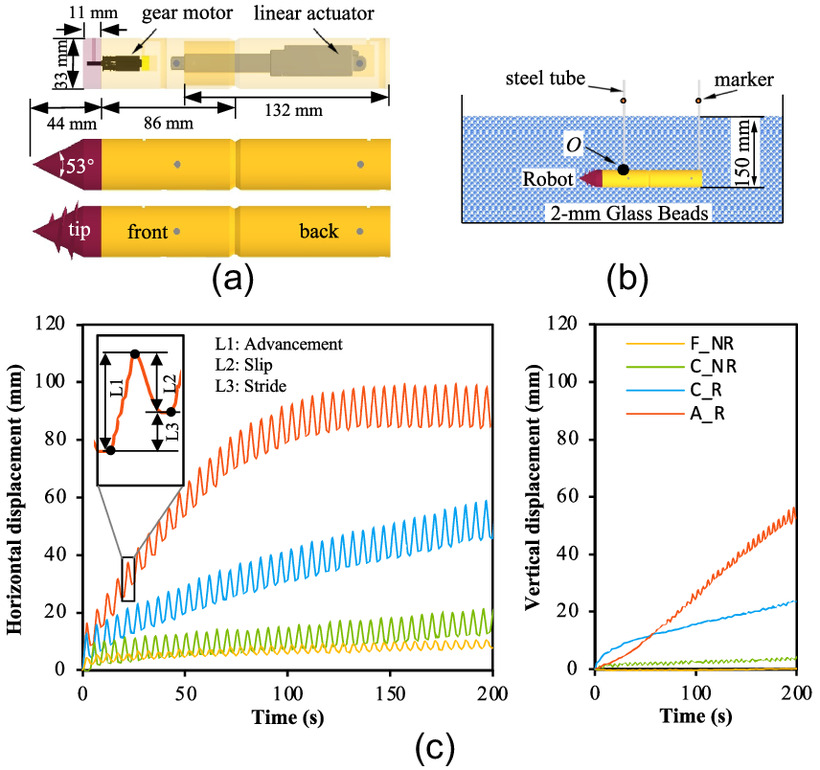
Four burrowing scenarios were tested with different combinations of tip shapes and kinematics. Tip shapes included a flat plate (F), cone (C), and auger (A), and tip kinematics included rotation (R) and nonrotation (NR). Each movement cycle of the robot had a duration of 5 s, including 2 s of extension, 2 s of contraction, and 1 s of pause with the linear actuator deactivated. In the C_R and A_R cases, the tip rotated at 100 rpm in the counterclockwise direction only during the extension phase. Each burrowing scenario was tested three times, and the results showed excellent repeatability.
During each burrowing cycle, the front section of the robot moved forward (advanced) during extension and moved backward (slipped) during contraction, resulting in a net movement (stride) [Fig. 1(c)]. The robot with the flat plate (F_NR) was the control case, as it represented a nearly symmetric design and yielded negligible net movements. With a non-rotational cone tip, the robot was no longer symmetric in shape, and it moved forward slightly. With a rotational cone tip, the kinematics was also asymmetric, and the robot moved faster and farther. With a left-handed auger tip, the asymmetry in shape and kinematics was further enhanced and yielded the fastest burrowing rate ( during the first 65 s) and the greatest distance (85 mm). In addition, vertical movements and tilting were observed for all asymmetric cases, which can be attributed to the vertical stress gradient in the soil analog. In the A_R case, the horizontal burrowing rate decreased gradually after 65 s as the robot tilted and moved closer to the surface. After 120 s, its horizontal movement became negligible, but the robot continued to tilt and moved vertically until the tip burrowed out to the surface.
Implications
Tao et al. (2019) demonstrated that, as a result of cyclic extension–contraction, a vertically aligned robot will burrow upward due to the asymmetric soil stress state and displacement constraints at the top and bottom of the robot. For a horizontally aligned robot, net horizontal movements are achieved by breaking the symmetry of the robot shape or the movement kinematics, or both. The burrowing speed increases with increasing degree of asymmetry. All the symmetry-breaking features that allow a reciprocating robot to advance seem to point to a single factor: the asymmetric load–displacement responses at the two ends of the robot. Further work is underway to test this new hypothesis.
Acknowledgments
The authors appreciate the support from NSF CMMI (#1849674).
References
Tao, J., S. Huang, and Y. Tang. 2019. “Bioinspired self-burrowing-out robot in dry sand.” J. Geotech. Geoenviron. Eng. 145 (12): 02819002. https://doi.org/10.1061/(ASCE)GT.1943-5606.0002177.
Information & Authors
Information
Published In
Copyright
© 2023 American Society of Civil Engineers.
History
Received: Nov 7, 2022
Accepted: Dec 15, 2022
Published online: Feb 9, 2023
Published in print: Apr 1, 2023
Discussion open until: Jul 9, 2023
Authors
Metrics & Citations
Metrics
Citations
Download citation
If you have the appropriate software installed, you can download article citation data to the citation manager of your choice. Simply select your manager software from the list below and click Download.